Cycleops
Legendary Member
- Location
- Accra, Ghana
I’m currently involved restoring an old Trek 1000 SL which I found down here much the worse for wear. Everything is there except the back wheel. I bought a ‘Home used’ one as they call it ( means it was brought into the country used) with a free hub appropriate for eight speed as original. The trouble is the rim doesn’t run central in the frame. My cycle repair guy says no prob just put spacers to shift it over, which we did but this makes the axle too wide and it’s a barsteward to get in now.
I thought you can dish the wheel by loosening the spokes one side and tightening them on the other but he say no. I thought this possible but is it?
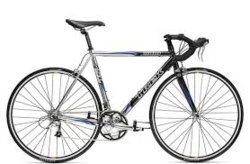
I thought you can dish the wheel by loosening the spokes one side and tightening them on the other but he say no. I thought this possible but is it?
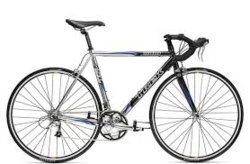
Last edited: